Environmentally Friendly PCB Design
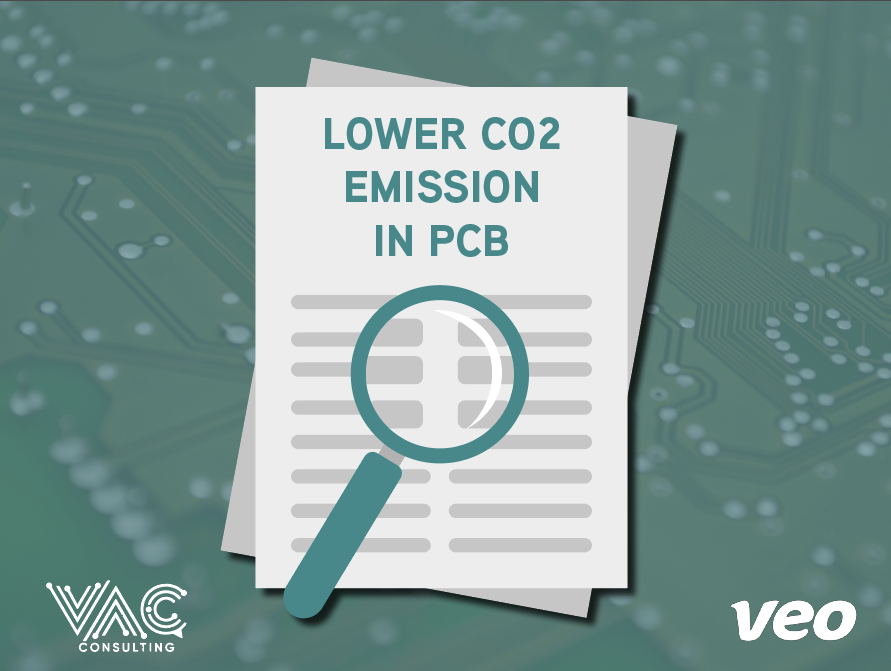
A Guide for Hardware Engineers and Their Managers
I (Anton Husby) have led hardware development teams in Soundboks and Veo. I found it to be a pain to understand DFM and Environmental considerations when my electronics designers design the PCBs (not the components mounted, I refer to this as PCBA). The industry is moving so fast and different suppliers have different preferences and methods of manufacturing and the weighing against design functionality and compliance made it an equation with too many unknowns, so my electronics engineers always gave up on trying to design perfectly for DFM and environmental footprint. This was not perfect enough for me when trying to reduce unit prices and reduce the environmental impact of my product, so I found a quite knowledgeable supplier named VAC Consulting. VAC does not own the PCB factories themselves but works with a handful of PCB suppliers that they have grown to know very well. They specialize in exactly what I was looking for, advising electronics designers on how to optimize their PCB designs for DFM and then they fix the production for you as well. I’m in general skeptical of middlemen, especially when trying to drive down the unit price, but I found that PCBs we estimated would cost around 15$/pcs could come down to a third of that by getting VAC’s input along the process. So, I’m quite happy about this partnership with VAC, and this article is written after a whiteboard session with them to also inform my engineers better in how to design for environmental impact. Around 70% of the CO2 emissions of a Veo Camera come from the PCB itself, and I know of many other product-companies with similar CO2 emission strain from their PCBs. So, this article is to hopefully inspire more companies to design for the environmental strain of your PCBs. It is not that difficult to take the first step – if you do it with VAC as your advisor you might even save money at the same time. (My engineers even have VAC starred in their phone-contacts, as they like collaborating with them so much)
Design Considerations Minimize the Number of Process Steps:
- V-cuts
- Reduce the number of routing bits by standardizing route widths to decrease the time required for bit changes.
- Threaded Holes: At Veo, we securely fasten components with threaded holes using our mechanical design.
- Blind/Buried Vias and other advanced technologies may add complexity and processing time. Laser drilling is a preferred method.
- Consider adopting a Flex-Rigid Stackup Symmetric (Flex Middle) approach to reduce waste and enhance durability. For instance, using hard gold for edge connectors like those on consumer RAM or GPUs can increase sturdiness.
- Whenever possible, utilize organic surface finishes like OSP.
PCB Production Panel Area Utilization:
- Reducing PCB area can maximize panel utilization, even if it means increasing the layer count (though be mindful of lead times).
- Organize a ‘Tetris meeting’ with your PCB manufacturer (or VAC) and your PCBA manufacturer to optimize the shape and placement of the PCB on the panel. Ensure that both the top and bottom sides can be handled simultaneously to avoid extra processes at your PCBA partner. Typical raw PCB panel sizes are 24” x 18”, and PCBA manufacturers work with various sizes depending on their machinery
Manufacturing Partner
- Require proper wastewater filtering.
- Some suppliers are developing systems to purify water to the point where it can be reused in production.
Gas:
- Demand that your supplier mitigates harmful emissions by filtering the gases produced during the acidic process steps of PCB manufacturing.
Shipping:
- Use recyclable or biodegradable packaging for PCB shipments.
- Consider the geographical location of your PCB manufacturer, your PCBA manufacturer, your final box assembly site, and your end customer. Reducing global shipping can save money and reduce environmental impact.
- Whenever possible, opt for sea transport as it is more environmentally friendly and cost-effective, especially for larger volumes.
Reduce, Reuse, Recycle
- A modular approach facilitates easier upgrades without replacing the entire PCB, reducing electronic waste.
Component Reusability:
- Design with component reuse in mind. Salvage and repurpose parts from decommissioned PCBs for other projects.
Recycling Programs:
- Collaborate with e-waste recycling programs to ensure that discarded PCBs are processed in an environmentally friendly manner.
X-out Policy:
- In PCB production, an X-out policy is common and allows for a certain percentage of defective PCBs in a panel. Avoiding a zero X-out policy is environmentally friendly and cost-effective, as excessive X-outs lead to unnecessary waste and higher unit prices.
Life Cycle Analysis:
- Consider the entire lifecycle of the PCB, from material extraction to end-of-life disposal, to optimize each stage and reduce the overall environmental footprint.