[yarpp]
4 most common types of PCB materials
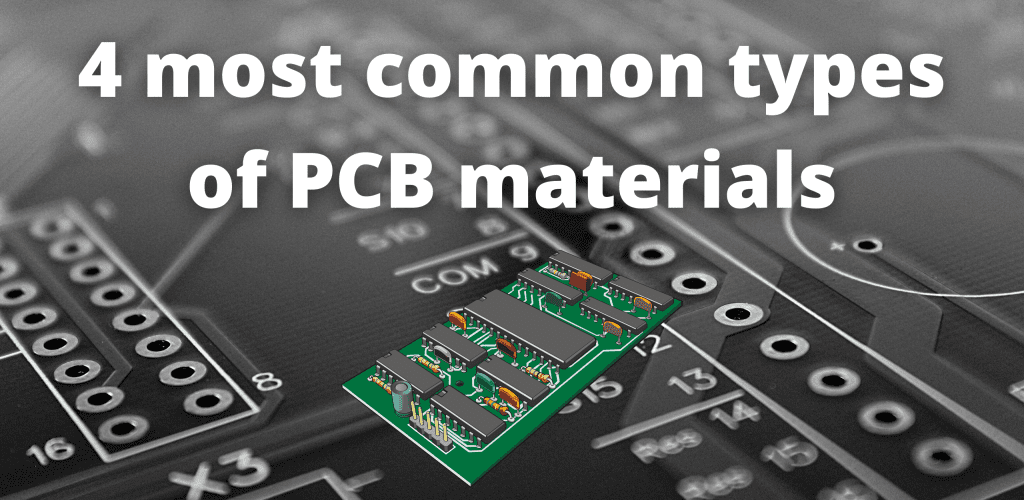
Back to basics - PCB Materials & what to consider when designing your solutions
Each PCB consists of 6 basic components:
- Prepreg → Insulation layer. Provided by a dielectric material that is between either 2 cores or a core and a copper foil.
- Laminate → A thin layer of different materials that are fused together using pressure and heat.
- Solder mask → A thin layer of polymer, to protect the copper from environmental influences, oxidation and shorts.
- Copper foil → Copper thickness that is applied on outer as well as inner layers of a multilayer PCB.
- Silk Screen → Ink traces used to identify components, test points, parts of the PCB, warning symbols, logos and marks etc.
- Surface finish → An intermetallic joint in the middle of the bare copper of the solderable area of the PCB and components
The different types of PCBs are as follows:
- Rigid PCBs
- Rigid-Flex PCBs
- Flex PCBs
- Single-sided PCB boards
- Double-sided PCB boards
- Multilayer PCB boards
- High-Frequency PCBs
- Aluminium-Backed PCBs
Hybrid PCBs
Another common hybrid variant is to include layers of Teflon materials within a conventional FR4 or polyimide PCB. The Teflon layers will provide the electronic designer with layers optimised for high speed signals, within an overall PCB package that is still manufacturable.
Low and No-Flow Prepregs
PCB Materials
- FR4
- Polyimide
- Metal
- Teflon
FR4 is a glass-reinforced epoxy laminate sheet that is both water-resistant as well as flame retardant. That paired with its excellent strength to weight ratio, makes it the most common fabrication material.
Polyimide laminated and prepreg, has a better performance compared to FR4 as well as a higher temperature performance. They are a more stable option during thermal cycling, and are suitable for a PCB with a high layer count. However, this is a more expensive option (If you want to read more about how you can keep your PCBs cost effective click here).
Metal has a much longer shelf life. The manufacturers use the traditional materials of iron, aluminium, copper and more. These materials allow SMT integration for components, and provide a great mechanical durability. As well as being; light weight, great heat dissipation, high-temperature stability all while being ideally, cost-effective. The advantages to a metalcore PCB is; Improved durability, light weight, good heat dissipation, stable under high temperatures, better LED density, good price.
Teflon does not provide any resistance, it is often used for both high-speed and high-frequency purposes. That is not the only point in its favor, the material is both very light and highly flexible making it the go to for a varied array of electronic solutions.
When designing your PCBs, be mindful of the materials and their properties. Your design can be perfect, but with the wrong material, they won’t live up to your designs full potential.
We can guide you from the design phase, through to your finished project.
In short, when designing your PCBs take the materials used in to heavy consideration. They are the building blocks to your layout, and if you have a sturdy foundation, you have already come a long way to making a strong, reliable and durable solution.
How to cost optimize your PCBs
In our work as consultants, we’ve been faced with this question many times “How can we make it less costly? What steps do we need to take for it to become a reality?”.
With our experience we have compiled a short list consisting of 7 pointers, that will help you in the right direction.
NOTE: these guidelines have been written with the object of cutting down the cost as much as possible. (This article is less relevant for highly complex boards)
- Area
-
- Area is THE most important part, when it comes to saving money! Your board needs to match that of the Assembly machines, while also having a good utilisation of the factory’s production panel.
- The more boards per production panel, the cheaper it’s going to be. Imagine a game of tetris. You have the background (the production panel in this example) where you need to fit as many pieces in as possible, to score the highest amount of points. Here it’s about how many boards you can fit onto a panel.
- This can be a difficult process that needs to be done properly, but a very necessary one! It’s one we are highly skilled in, and our expertise can save you both time and money. We work closely with the Assembly and the PCB factory, to ensure the process runs smoothly.
- Stack up
-
- What materials can I use? Go for the factory’s standard material with the lowest TG value. They buy it in bulk and are therefore able to offer it to you at a lower cost.
- Be aware of your measurements of each layer. You may have specific requirements to your stackup, but the choice of your dielectrics may not correlate with the stock at the factory, so they have to purchase. It will add to lead time and cost.
- Keep it to the standard 1.0 mm or 1.6 mm. Any other will be subject to additional costs.
- Keep your stack up symmetrical and refrain from mixing different brands of materials. It is not conducive to saving money, quite the contrary. It makes the production process much more difficult, and therefore increases both lead time and cost.
- Tracks
-
- What is the factory standard? If the goal is to save costs, then it is not recommended to go below the factory’s standard track width + space.
- Avoid impedance control. You can still make your single and diff. pairs. The added cost only shows up when you ask the factory to control whether or not the impedance is what you request. If you are confident in your tracks and ohm calculations, or if your tolerance is within such a high margin that it doesn’t really matter, then you can still make the tracks.
- Holes
-
- What is the standard for the factory? Never go below their standard hole size + annular ring.
- To save costs, you should avoid HDI technology altogether. The process of HDI will add additional pressing stages. It will add to longer lead time, and higher costs.
- Avoid both blind & buried, as well as special technologies, backdrilling etc.
- Surface treatment
-
- The cheapest is alway LF HASL, HOWEVER! It depends on mounting and components.
- If the components are mounted with a very little distance, LF HASL is impossible to do, it then needs to be ENIG or more advanced. This in turn will add to the cost.
- LF HASL stands for “Lead free hot air solder levelling”. It is low-cost, available and repairable. This is the cheaper option.
- ENIG is a double layer metallic coating, with nickel being used as both a barrier to the copper and as a surface where the components are soldered on. This is the more expensive option.
- There are many surface finishes available, all of them with their own list of pros and cons in terms of production and assembly (an article for another time.) However, nearly all of them are more time consuming and at a higher price point than the commonly used LF HASL
- Milling
-
- There are 2 types of milling: V-cut & milling
- V-cut: If the long game is to save money, make sure your design is made so everything can get V-cut. However, there can be some disadvantages to this method. You can’t do this if your design has an abnormal shape, as it can only cut in straight lines. Another disadvantage is the fact that you have to “break out” the print, and this can cause some sharp edges.
- Milling: The most usual milling type. It is a necessity for designs with rounded edges, unusual shapes, and if it needs milling inside of a print. Too much milling can add to, not only the delivery time, but also the cost.
- The most expensive solution is to do a mix of both, as two different processes will need to start.
- Keep to only 1 of the processes; V-cut is the cheapest, Milling is standard, and a mix of both is the most expensive.
- Solder mask/Silkscreen printing
-
- This is not where you are saving a lot of money. Keep to these pointers, and the cost will remain low.
- Go with the standard solder mask in green. Changing the colour of the solder mask is going to add to the cost.
- To save money on a 1 layer board, only add a solder mask on the side where there is no copper. The only disadvantage is an “ugly” print, because the one side will only be orange/brown.
- This only makes sense when producing a lot of boards.
- Keep the white colour when silkscreen printing. It is one of the last processes and is, essentially, just an Inkjet printer, that prints text onto the print itself. Different colour text will add to the cost.
- To have the text done in copper or silkscreen, will cost the same.
- REMEMBER! The more text, the less space and the higher chance for the text to cover pads.
As this list shows, there is a lot to keep in mind when saving money is the name of the game. Not only that, but this process also requires a vast amount of correspondence between you, your PCB factory and your Assembly. This in turn has the potential to take away both time and resources from your project.
But that’s where we come in. All of the above, is what we handle! By shifting these aspects of your projects over to us, we can save you both time and money, as well as solve any disputes that may arise. Allowing us to take this workload, allows you to remain focused on developing your solutions!
Let’s have a short recap!
To cut down cost, keep it simple and with conventional shapes, trust that your calculations are correct and get in touch with us, to avoid making any costly mistakes and free up your own time to focus on your projects.
[yarpp]